- Job Seeker Resources
- |
- Last Updated: February 08, 2023
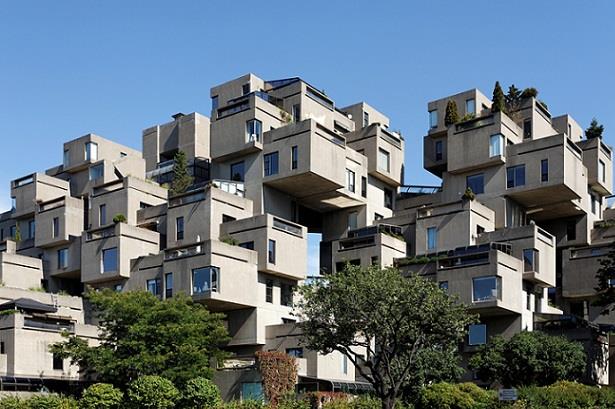
5 Pros of Modular & Prefabricated Construction
Modular and prefabricated (prefab) construction is a method that involves several of a building’s components built in an offsite factory and assembled on site at an optimal time. If this only brings to mind trailer homes and school portables, think again: modular and prefab techniques are being applied to a wide range of industrial, commercial, and residential buildings with the potential to deliver the following benefits:
1. Reduced environmental impact
As reported by The Modular Building Institute’s white paper, “Improving Construction Efficiency and Productivity with Modular Construction,” more than 135M tons of debris from construction sites in the US end up in landfills every year. Prefab and modular techniques enable the reduction in material waste as well as air and water pollution and overall energy usage. Additionally, the USGBC awards credits specifically for homes that use offsite fabrication for walls, roof, and floors as part of their LEED for Homes rating system.
2. Increased worker safety and productivity
Modular and prefab construction can alleviate onsite hazards such as height- and confined space-related dangers. Spending less time on site also means less exposure to inclement weather and extreme temperatures. Plus, controlled factory conditions support enhanced productivity, precision, and quality.
Find your next great opportunity. Register with iHire.
3. Streamlined onsite materials and waste
According to an AMA Research Ltd. report published by Waste and Resources Action Programme (WRAP), “Current Practices and Future Potential in Modern Methods of Construction,” offsite manufacturing has the potential to save up to 90% in onsite waste related to packaging, temporary, and damaged materials. Onsite theft also decreases, as whole modular units are a lot harder to steal compared to smaller, individual parts.
4. Faster project completion
As an expected result of the benefits listed above, projects are completed more efficiently. With work being performed off site, onsite tasks can occur simultaneously and allow for a compact schedule. Additionally, onsite weather delays cease to be a major problem.
Graphic source: http://www.modular.org/marketing/documents/Whitepaper_ImprovingConstructionEfficiency.pdf
5. Flexibility and adaptability
Modular building parts are often designed in a way that allows for them to be readily disassembled, moved, and/or refurbished for new use. As per The Modular Building Institute’s white paper, some modular buildings can even be recycled in their entirety.
Is there any reason NOT to go modular? At this point in time, there are a few overarching cons: slow-to-adapt building codes and zoning rules, restricted design customization, and the extra coordination necessary between offsite and onsite teams (including the need for a conveniently located offsite factory). However, as a strategy with more pros than cons (particularly its “green” benefits), the popularity and widespread use of modular and prefab construction will likely be ever increasing.
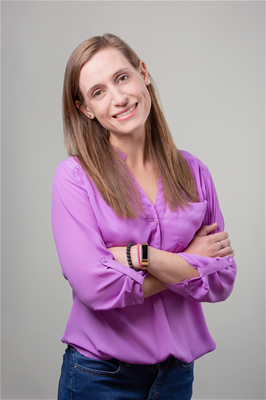
Originally Published: October 30, 2015
Sign In or Register to access all articles and insider tips for help in your job search.
Search for Construction Jobs
RELATED JOBS
Job Posting: Since 1953, Ferguson has been a source of quality supplies for a variety of...
Structural Engineer SEPosition Summary Actalent connects passion with purpose. We are supporting critical engineering...
Electrical Engineer/Technologist - Electrical Engineer/Technologist SeniorJob Posting End Date 07-14-2025 Please note the job posting will close on the day before the...
Line Mechanic DJob Posting End Date 07-14-2025 Please note the job posting will close on the day before the...
Infrastructure Engineer Senior - PrincipleJob Posting End Date 07-13-2025 Please note the job posting will close on the day before the...
RELATED RESOURCES
Find the Right Job Faster
- Get personalized job matches sent to your inbox every day
- Connect directly with employers before your competition
- Advance your career with expert advice on interviewing, salary negotiation, and more
We value your privacy